Our view at Stack - Shopify has just about everything you need if you're looking to sell online. It excels with unlimited products, user-friendly setup, and 24/7 support. It offers 6,000+ app integrations, abandoned cart recovery, and shipping discounts up to 88%. Plus, it allows selling both online and in-person, scaling as your business grows.
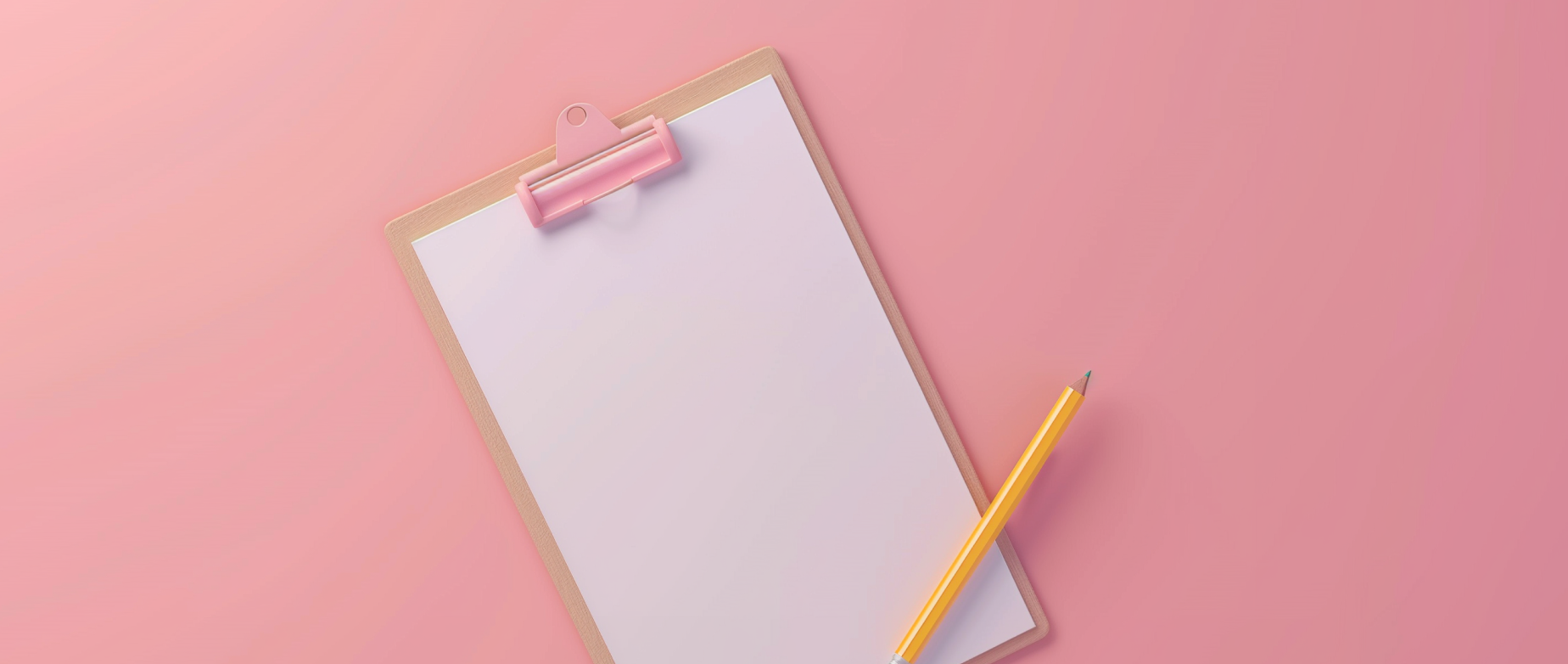
Imagine three friends, all avid cyclists, who decide to start a business making bicycles. They have conducted market research and expect the US bicycle market to increase in size during the next several years. They’re considering setting up a manufacturing business, not just a makeshift workshop in the back of a bike store. To do this, they need to start production planning—an essential component of the manufacturing process.
What is production planning?
Production planning is part of a manufacturing strategy that details how much capital, labor, raw materials, and manufacturing space a company needs to make enough goods to meet customer demand. The production planning process also helps a business see where problems might occur, determine how to solve them, and keep producing on schedule for delivery to buyers.
Production planning organizes all aspects of manufacturing while improving communication and cooperation among employees, suppliers, and contractors. It also helps with the efficient allocation of resources, reducing costs, and managing the supply chain.
Production planning vs. production scheduling
Production planning and production scheduling are both steps in the production process, but they are different. Production planning determines what and how much a company produces, while scheduling, a part of the planning process, determines when and by whom various production tasks are completed.
Production planning methods
The various types of production processes depend on product type and scale. Some are intermittent processes, with periods when a company produces nothing, while others are continuous, where production is rarely or never interrupted. Some of the most common production planning methods include:
Job method
The job method, also known as the project method or shop method, is usually for making a single product with unique features. Smaller examples of job-method production are made-to-order furniture, custom-tailored clothing, and one-of-a-kind jewelry pieces. On the larger side, this could be a custom home or yacht.
Job production is typically a labor-intensiveproduction process, and each unit is different. It’s the opposite of mass production, where companies make large quantities of uniform products through automated processes at lower cost. Also unlike mass production, there are commonly no economies of scale, because each job and each product is different rather than the same.
Batch method
Batch production is the manufacturing of identical goods in groups. Examples of batch production include baked goods, basic clothing such as t-shirts and socks, and print publications such as newspapers and books.
The batch production planning process focuses on determining the right amount of output, avoiding overproduction or underproduction. A sock manufacturer, for instance, doesn’t want to produce 1,000 pairs when there’s demand for only 500.
For some businesses, batch production can increase efficiency. The sock maker might set the machinery to produce 500 pairs of black socks, then quickly switch to a batch of 500 gray pairs, and switch again to 500 dark blue pairs, knowing those are the three most popular sock colors. A batch manufacturer wants to minimize changeover time between batches because delays and bottlenecks between product runs can become costly.
Flow or mass-production method
Flow production, also called mass production, is a manufacturing process for standardized goods defined by the continuous movement, or flow, along a factory assembly line. This is generally an automated process with minimal human intervention, which makes it quick and cost-effective compared with job or batch production. An automotive plant is a good example; car or truck assembly flows through various steps on the production line toward completion. Processed foods, such as canned soup or even bread, are another example.
Setting up this type of production process requires a significant capital investment, generally limiting its use to larger companies.
The two main principles of flow production are extensive automation and division of labor—each employee has a specific task in the production process. This differs from batch or job production, where employees may handle multiple tasks.
Process method
The process method is similar to the flow method—both use continuous production. A key difference is that process production typically uses raw materials to turn out bulk goods or commodity goods, such as liquids and gasses, rather than discrete products such as individual cars or cans of food. Refined oil products and chemicals are examples of process products.
Careful planning for process manufacturing is essential because of the potential for overproduction or underproduction.
How to make a production plan
- Forecast demand
- Make a budget
- Create a production sequence
- Set a production schedule
- Control and evaluation
The production planning process involves developing a comprehensive overview of your business. Here are the key steps in putting together a production plan:
1. Forecast demand
Start by estimating production requirements based on predicted customer demand. Historical sales data can help with demand forecasting, but you’ll also need to consider other factors that can affect demand, such as recent market trends and how economic conditions affect your customer base. Market research can help you predict whether demand for your product is changing, and this can influence your production plans.
Production planning software for demand forecasting can help guide your decisions about matching production and demand. The software also typically tracks inventory, which can influence your planning for producing new goods.
2. Make a budget
Budgeting helps to identify the cost of resources needed to produce your desired output. This includes materials, facilities, and workers. Your current production capacity—the maximum you could reasonably produce with available staff, materials, and facilities—will inform your production plan.
3. Create a production sequence
Mapping out the production process and the steps required to produce your goods includes buying any necessary equipment and tools—or outside services. Depending on the type of production, some steps in the process may be done simultaneously, some must be done one at a time, and others may be outsourced.
Production planners can also use the production sequencing phase to prepare for contingencies such as equipment breakdowns, staff shortages, or supply interruptions.
4. Set a production schedule
Production scheduling is where you assign tasks to your various employees or teams, communicate the production plan to everyone involved, and set timelines for each stage of production.
Create a detailed production schedule that spells out how the company will execute the plan, including the resources and timing for each step. Production schedules keep manufacturing on pace and help a company avoid common production planning mistakes, such as overproducing or underproducing.
5. Control and evaluation
Once production starts, you’ll need to track performance and continually compare it to targets described in the production plan. Key performance indicators (KPIs) are the most relevant measures to track. In the case of a manufacturer, they can include the rate of production, such as the number of cars assembled per day and downtime, or the amount of time when nothing is being produced.
Carefully monitoring the production process can help you detect any issues and correct them quickly. It may also help you see ways to improve the manufacturing process after production starts, letting you build in some wiggle room for equipment breakdowns, supply-chain disruptions, or product defects.
Production planning FAQ
What are production planning KPIs?
Production planning key performance indicators (KPIs) help manufacturers track their processes by comparing them to goals or targets. Production KPIs include production rate, rejection rate of faulty products, and downtime, when production is halted for reasons such as broken machinery.
What is an example of production planning?
An example of production planning might be a bicycle manufacturing business. The company forecasts demand for bicycles, budgets for average production costs, arranges for materials and labor, and proceeds with plans to build a certain number of bicycles per month. After it begins making bicycles, it compares the results against the goals in the production plan and makes adjustments as needed.
What do production planners do?
Production planners organize a manufacturer’s main activity—turning out products. Production planning is a complex process, requiring constant communication with the other divisions of the business such as sales, finance, and human resources. A planner tries to set achievable production goals, while allowing some room for contingencies such as equipment breakdowns, supply-chain snags, or a lack of workers.
If Shopify is of interest and you'd like more information, please do make contact or take a look in more detail here.
Credit: Original article published here.